Hybrid Systems and How They Enhance Biomechanics Research
In our last posting, we outlined several topics that clients have been requesting over the years as ways to extend and deepen the area of motion capture and biomechanics research. One area we discussed briefly was Hybrid systems.
Hybrid Systems: Only a few clients have actually said, “We need a ‘hybrid system.’” But lots of you have said, “I wish I could have the unique advantages that each technology offers in one package.”
It is widely recognized that different technologies have different advantages and disadvantages. Putting technologies together to take advantage of the strengths that each technology offers is what makes hybrid systems so important.
What exactly is a hybrid system? In plain English, it is a system that can switch between technologies. A hybrid car that runs on gas or on electric is an example. In the world of motion capture, a hybrid system is one that can use two technologies for the same purpose. It is a system that can seamlessly switch from using one technology to using a second technology.
One supplier of optical systems, Vicon, recently announced the ability to collect their optical data and inertial measurement units (IMU) data thru Nexus. We would not classify that as a hybrid system, though I suspect they might offer a hybrid system in the future. For now, it is simply collecting two technologies in the same software…something akin to collecting forceplates or emg in the same collection session. In The MotionMonitor xGen, a hybrid system might use both optical and IMU data to track body segments and switch from optical (more accurate) to IMU (no line of sight requirement) when the optical markers are temporarily occluded. Essentially it is a system that is better as a result of the advantages offered by each of the technologies.
The variety of tracking technologies exist because each offers some advantage over competing technologies. Optical tracking is generally considered more accurate but if line of sight issues exist because of the complexity of the activity or limitation on the number of cameras, other technologies that do not require line of sight may be preferable. Workplace settings may be particularly susceptible to line of sight issues as shown in this demonstration video.
Differences in the form factor of technologies is another reason for using a hybrid system. Using tiny reflective markers to track finger movement can be complicated by a number of causes.
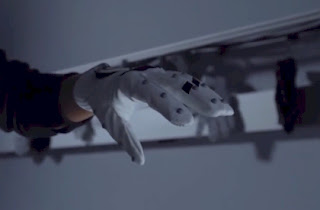
Finger dexterity can create line of sight issues. The physical presence of objects on the external surface of fingers can interfere with activity. The small sized markers may limit the volume in which the activity can be tracked. And given that marker data is only 3DOF means that only position and not orientation can be tracked with each marker. To obtain orientation data, each marker would be replaced with a rigid body of 3 markers further complicating tracking and interfering with finger movement.
With The MotionMonitor xGen we might substitute, Ascension or Polhemus’ mini 6DOF electromagnetic sensors for markers for this application.
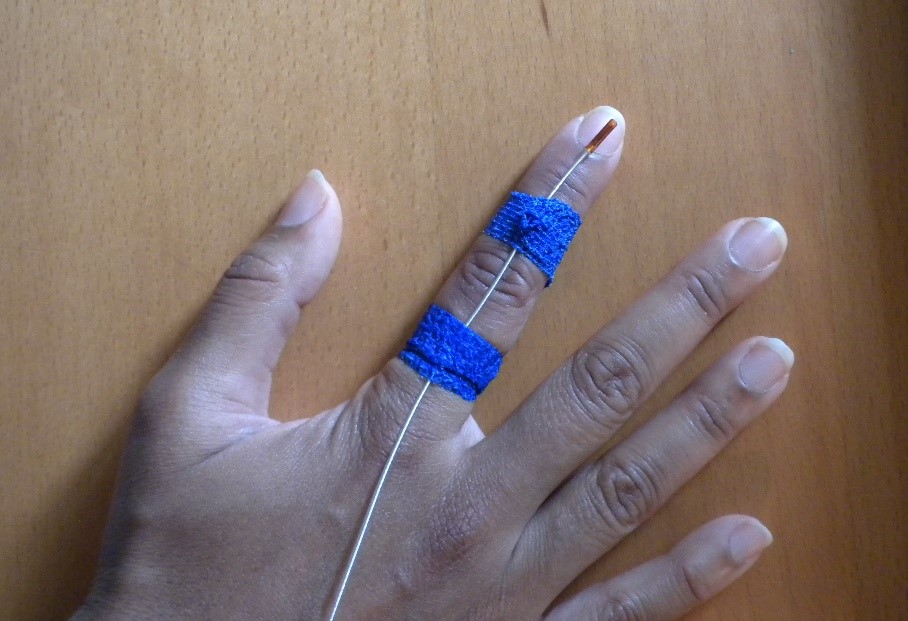
Line of sight is not an issue with these sensors and they provide both position and orientation enabling the use of a single sensor to track the entire finger motion. When used inside surgical or sporting gloves these sensors are nearly imperceptible. Dr. Carla Pugh has used this technology as part of her simulation engineering for surgical education lab at the University of Wisconsin.
In this demonstration video, a hybrid system consisting of a PhaseSpace active optical system is used to track upper body while Ascension 2mm sensors track the fingers.
Another reason for using a hybrid system is related to the complexity of defining the biomechanical model. Some technologies are easier to transform from the rigid body’s position and orientation to the subject’s anatomical joint centers and coordinate system. For example, IMU’s only provide orientation data. As a result, subject setup requires a tedious physical measurement of segment lengths and the creation of a model within the software. A hybrid system can greatly simplify the process. A stylus tracked with an optical system can be used to duplicate methods from our optical or electromagnetic systems. Subject segment endpoints and landmarks are simply digitized resulting in easier, faster and much more accurate biomechanical model. In this video an optical digitizing stylus is used to locate landmarks on a subject instrumented with Xsens IMU’s.
It is worth noting that this might sound like a high cost approach to using a low-cost technology (both optical and IMU systems being required), however, there are low cost, small volume, optical systems that can be used effectively. There are many solutions for this, the Optitrack Trio shown here is an example. This raises another reason for hybrid; a combination of technologies can provide the ability to expand an existing study or capture a new application without requiring a full hardware replacement or extensive additions, like multiple cameras or larger transmitters. A hybrid approach provides unique solutions at a different price point and may have a cost advantage over the traditional approach, depending on the situation and application.
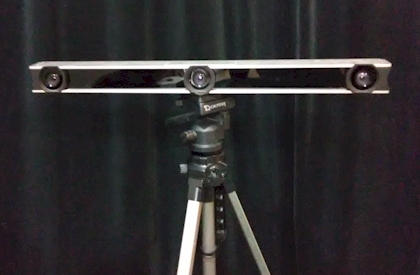
In summary, it may not yet be possible to have all the advantages of the diverse tracking technologies in one hardware package, but it is possible to combine different technologies via software. Hybrid systems offer a novel, modern solution to many biomechanical questions.
Let us know where you see potential for the application of a hybrid system.
-Meredith